Supply of oily water treatment systems
THE HORIZONTAL FLOTATION UNIT USING DISSOLVED AIR OR GAS
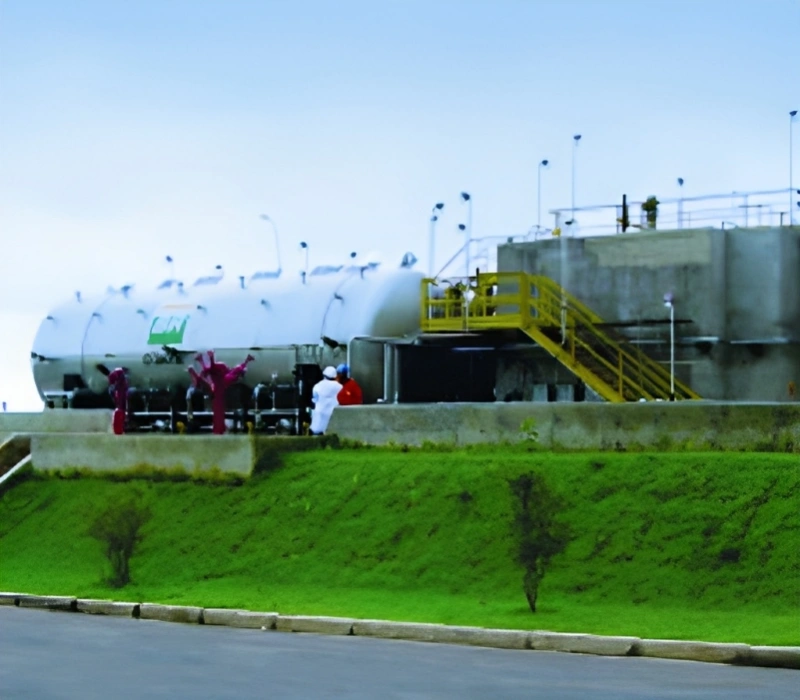
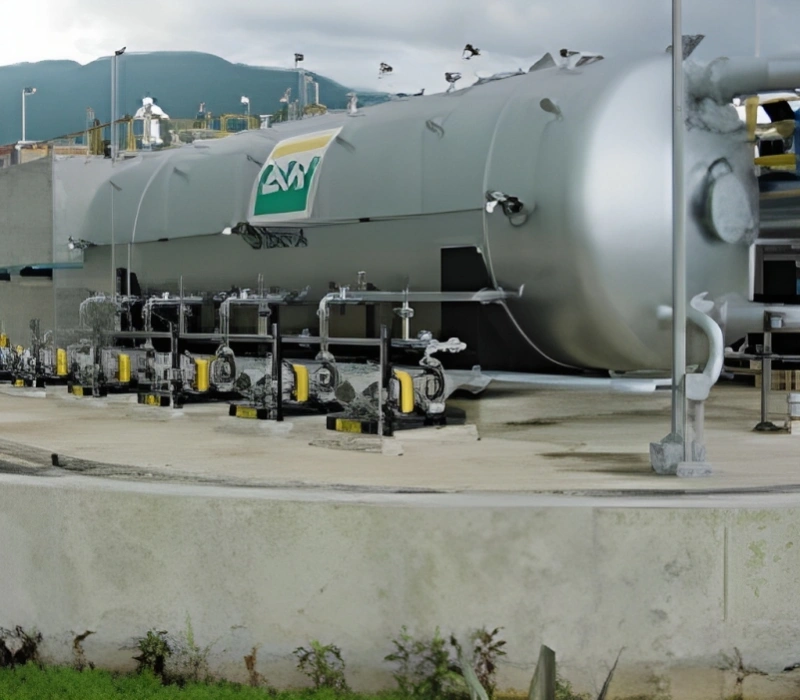
Model type
- The Veirsep Flotation Unit
Characteristics
- A compact horizontal wastewater treatment process consisting of a fabricated steel vessel operating in cells at atmospheric or positive pressures.
- It is a totally automatic system
- Very high efficiency
- The basic structure consists of the following component parts: a Spiralsep centrifugal separator, seven independent working cells, a coalescing section, an oil channel and the DGF pumps that besides pumping fluid generate air/gas bubbles. Other ancillary components as necessary for operation and automatic process control.
DGF Dissolved Gas Flotation Pumps
DGF pumps circulate fluid drawn from one end of the flotation system chamber into the unit’s central cells or chambers. Impellers are designed to entrain atmospheric air (or a flotation gas) into the fluid stream and cause it to dissolve in the form of minute bubbles.
These special pumps permit control of the aeration bubbles, the diameter of which varies from a micron upwards. An individual pump with its respective controls serves each operational cell.
Advantages
- Compact design needing relatively small space and a minimum of installation works.
- As a closed system it is free of aerosols and smells
- In contrast to conventional separators there are no mechanical or rotating cleaning devices, a design feature that guarantees uninterrupted operation as well as reducing running costs.
- Compressed air is not used and there is no saturation chamber as is common with other systems. This power saving reduces costs directly and indirectly by having fewer ancillary devices and correspondingly less maintenance.
- A further Power saving comes from the recycling process, which is less than 20% of the total flow, whereas 50% is a common value with other systems.
- Precise and individual control of the micro bubbles in each of the unit’s cells gives effective and efficient control over the flotation process.
- The quantity of polyelectrolyte, used in the coalescing stage, is about half that used in other processes. An economy resulting from high performance of the DGF pump.
- Total oil and grease (TOG) in outlet water is 20 ppm.
- Very low water content in reclaimed oil dispenses with subsequent separation processes.
- The unit’s capacity for accommodating large flow variations means operational flexibility.
- Low operational costs based on a fully automated design.
- Low maintenance costs
- Straightforward erection and rapid start-up procedures.
THE VERTICAL FLOTATION UNIT USING DISSOLVED AIR OR GAS
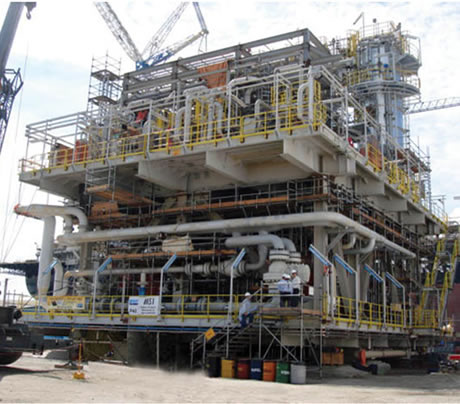
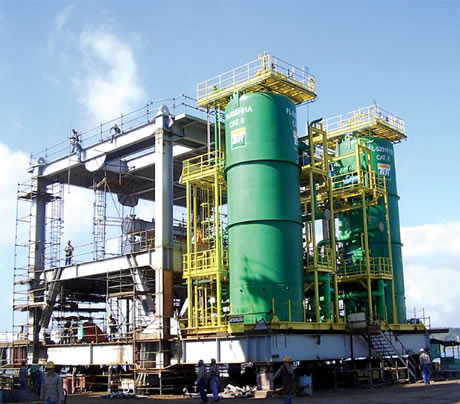
Model type
- The Spinsep Flotation Unit
- The Cyclosep Flotation Unit
Characteristics
- Compact vertical wastewater treatment process consisting of a fabricated steel vessel operating at atmospheric or positive pressures.
- It is a totally automatic system.
- This unit has a Spiralsep centrifugal separator, a hydro-cyclone, a flotation chamber, a coalescing section, an oil collector and the DGF pumps that besides pumping fluid generate air/gas bubbles. Other ancillary components as necessary for operation and automatic process control.
- Very high efficiency.
- For FPSO installations subject to ocean swell, the unit is equipped with wave compensation device for a vessel roll (up to 10o) it also prevents water spilling into the oil collector.
DGF Dissolved Gas Flotation Pumps
DGF pumps circulate fluid within the flotation unit and entrain atmospheric air (or a flotation gas) into the fluid stream, causing it to dissolve in the form of minute bubbles, the diameter of which varies from a micron upwards. The bubble size can be varied to achieve best efficiency.
Advantages
- Compact design needing relatively small space and a minimum of installation works.
- As a closed system it is free of aerosols and smells
- In contrast to conventional separators there are no mechanical or rotating cleaning devices, a design feature that guarantees uninterrupted operation as well as reducing running costs.
- Compressed air is not used and there is no saturation chamber as is common with other systems. This power saving reduces costs directly and indirectly by having fewer ancillary devices and correspondingly less maintenance.
- A further Power saving comes from the recycling process, which is less than 20% of the total flow, whereas 50% is a common value with other systems.
- The quantity of polyelectrolyte, used in the coalescing stage, is about half that used in other processes. An economy resulting from high performance of the DGF pump.
- Total oil and grease (TOG) in outlet water is 20 ppm.
- Very low water content in reclaimed oil dispenses with subsequent separation processes.
- The unit’s capacity for accommodating large flow variations means operational flexibility.
- Low operational costs based on a fully automated design.
- Low maintenance costs
- Straightforward erection and rapid start-up procedures.